Benefits
- Higher product quality and reduced series ramp-up costs
- End-to-end process from defect recording through troubleshooting to solution archive
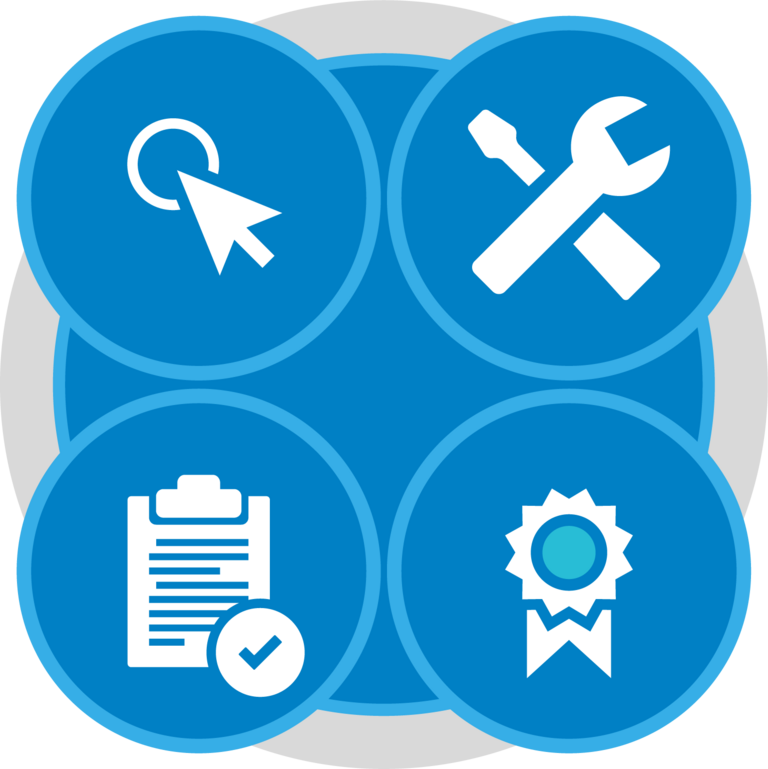
Increase your product quality and reduce your series ramp-up costs through integrated defect management
CONTACT Elements Quality Issue Management enables efficient processing of problem reports during test procedures, in series ramp-up and from production directly in the product or project context. Compliant with quality standards such as EN ISO 9001 and ISO 16949 with regard to the requirements for documentation and traceability of complaints, you process complaints and rectify product defects. You benefit from higher customer satisfaction thanks to improved product quality as well as from reduced series start-up costs and faster series maturity thanks to targeted troubleshooting.
Increase your product quality and reduce your series ramp-up costs through integrated defect management
CONTACT Elements Quality Issue Management enables efficient processing of problem reports during test procedures, in series ramp-up and from production directly in the product or project context. Compliant with quality standards such as EN ISO 9001 and ISO 16949 with regard to the requirements for documentation and traceability of complaints, you process complaints and rectify product defects. You benefit from higher customer satisfaction thanks to improved product quality as well as from reduced series start-up costs and faster series maturity thanks to targeted troubleshooting.
CONTACT Elements Quality Issue Management enables efficient processing of problem reports during test procedures, in series ramp-up and from production directly in the product or project context. Compliant with quality standards such as EN ISO 9001 and ISO 16949 with regard to the requirements for documentation and traceability of complaints, you process complaints and rectify product defects. You benefit from higher customer satisfaction thanks to improved product quality as well as from reduced series start-up costs and faster series maturity thanks to targeted troubleshooting.
Implement an end-to-end process from the recording of errors to their rectification through to the archiving of solutions
With Quality Issues, implement an automatically initiated process to respond to the occurrence of product defects or errors. To do this, use standardized workflows to store best practices and guidelines that map your solution strategies to your processes. This enables you to record and evaluate errors efficiently and speed up error correction measures through checklists, tickets, direct access to test reports and certificates, for example for supplied parts, as well as through links between defects and the actions taken to remedy them. Extensive analytical capabilities, the construction of a solution archive based on the history of actions and a direct link to CAD, ERP and customer master data make Quality Issues the basis for your efficient quality and defect management approach.
With Quality Issues, implement an automatically initiated process to respond to the occurrence of product defects or errors. To do this, use standardized workflows to store best practices and guidelines that map your solution strategies to your processes. This enables you to record and evaluate errors efficiently and speed up error correction measures through checklists, tickets, direct access to test reports and certificates, for example for supplied parts, as well as through links between defects and the actions taken to remedy them. Extensive analytical capabilities, the construction of a solution archive based on the history of actions and a direct link to CAD, ERP and customer master data make Quality Issues the basis for your efficient quality and defect management approach.
Related Elements
Fulfilling requirements to the letter
Document best practices in a digital library
Use proven methods and sets of guidelines such as CAPA, 8D or APQP
Give your employees a way to apply process-related knowledge easily and reliably
Proactive project risk management: safeguard projects through precaution and active control control
Safeguard projects through proactive risk management
Make risks visible and control them
Meet risk and quality management standards with less effort