Systematically planning and controlling complex production processes
Managing production processes is a complex challenge. The reasons for this range from the number and interlinking of production steps and the integration of the IT systems involved to the maintenance of production equipment and workforce scheduling. Manufacturing Operations Management (MOM) encompasses the broad spectrum of production-related functions, including the planning, scheduling and execution of production orders. CONTACT's MOM solution provides a transparent overall picture of your production processes. It seamlessly connects your product development with your production and thus enables end-to-end digital control.
Benefits
- Maximize availability of machinery and equipment
- Basis for continuous improvement of production processes
- Transparency from shopfloor to management
- Live data from production for smooth processes – from machine control to management reports
- Efficient support and flexible coordination of production teams
- Multi-site architecture for high performance across all locations
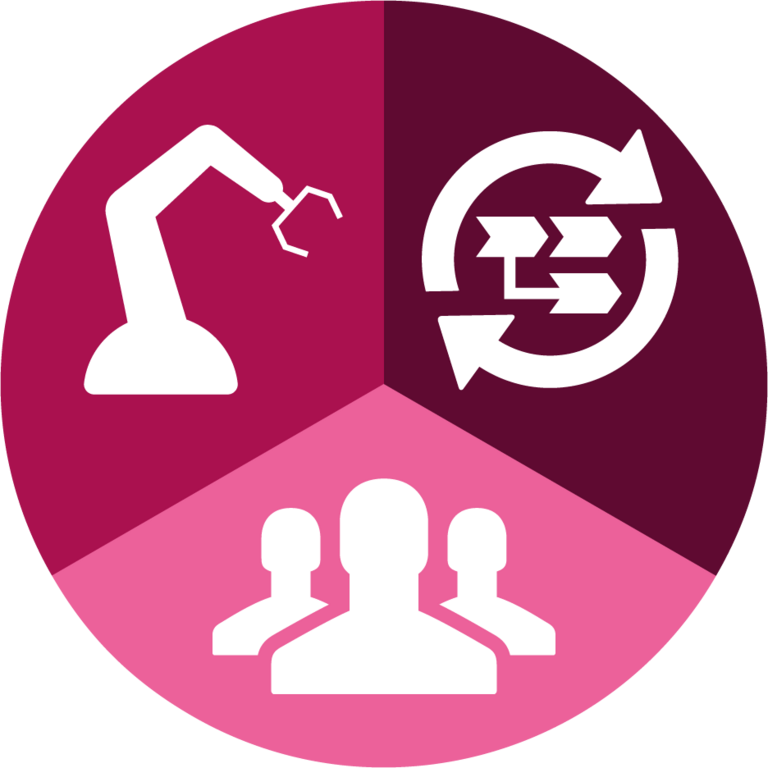
Maximize the availability and performance of your assets
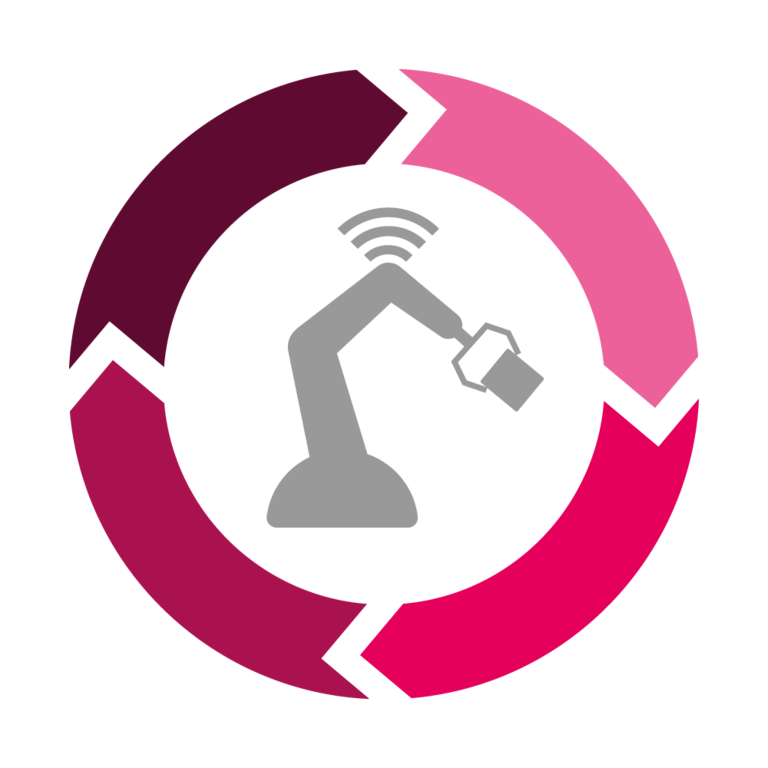
Enterprise Asset Management (EAM) enables you to map the complexity of your production in detail using digital twins. Use the as-maintained condition, including changes due to maintenance, as a basis for planning, implementing and documenting maintenance, repair and overhaul processes (MRO).
Dashboards provide you with an overview of the utilization of machines as well as personnel deployment, shift planning and maintenance. This enables flexible, demand-oriented maintenance planning that ensures high availability of your equipment. With real-time KPIs on production progress and a data-based control logic, you significantly reduce the coordination effort on the shopfloor and maximize the performance of your production.
Maximize the availability and performance of your assets
Enterprise Asset Management (EAM) enables you to map the complexity of your production in detail using digital twins. Use the as-maintained condition, including changes due to maintenance, as a basis for planning, implementing and documenting maintenance, repair and overhaul processes (MRO).
Dashboards provide you with an overview of the utilization of machines as well as personnel deployment, shift planning and maintenance. This enables flexible, demand-oriented maintenance planning that ensures high availability of your equipment. With real-time KPIs on production progress and a data-based control logic, you significantly reduce the coordination effort on the shopfloor and maximize the performance of your production.
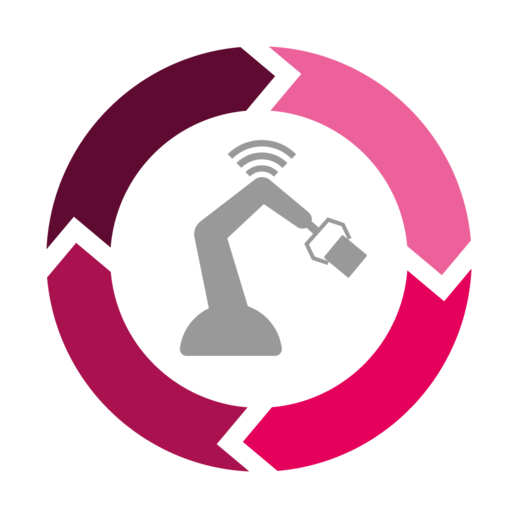
Enterprise Asset Management (EAM) enables you to map the complexity of your production in detail using digital twins. Use the as-maintained condition, including changes due to maintenance, as a basis for planning, implementing and documenting maintenance, repair and overhaul processes (MRO).
Dashboards provide you with an overview of the utilization of machines as well as personnel deployment, shift planning and maintenance. This enables flexible, demand-oriented maintenance planning that ensures high availability of your equipment. With real-time KPIs on production progress and a data-based control logic, you significantly reduce the coordination effort on the shopfloor and maximize the performance of your production.
Gain transparency from the shopfloor to the management level
The Shopfloor Navigator provides production and plant managers as well as shift supervisors with the appropriate information in clear dashboards. This means that you always have an overview of which customer order is currently being processed in which plant at which workstation and can immediately analyze the reasons for downtimes or rejects.
Transfer production orders with assignments for plants and shifts directly from the ERP system and expand them with live data from production such as machine control or sensor data. With these aggregated digital shopfloor files, you fulfill verification obligations, obtain starting points for automation and produce more economically.
Gain transparency from the shopfloor to the management level
The Shopfloor Navigator provides production and plant managers as well as shift supervisors with the appropriate information in clear dashboards. This means that you always have an overview of which customer order is currently being processed in which plant at which workstation and can immediately analyze the reasons for downtimes or rejects.
Transfer production orders with assignments for plants and shifts directly from the ERP system and expand them with live data from production such as machine control or sensor data. With these aggregated digital shopfloor files, you fulfill verification obligations, obtain starting points for automation and produce more economically.
The Shopfloor Navigator provides production and plant managers as well as shift supervisors with the appropriate information in clear dashboards. This means that you always have an overview of which customer order is currently being processed in which plant at which workstation and can immediately analyze the reasons for downtimes or rejects.
Transfer production orders with assignments for plants and shifts directly from the ERP system and expand them with live data from production such as machine control or sensor data. With these aggregated digital shopfloor files, you fulfill verification obligations, obtain starting points for automation and produce more economically.
Coordinate your production team efficiently and flexibly
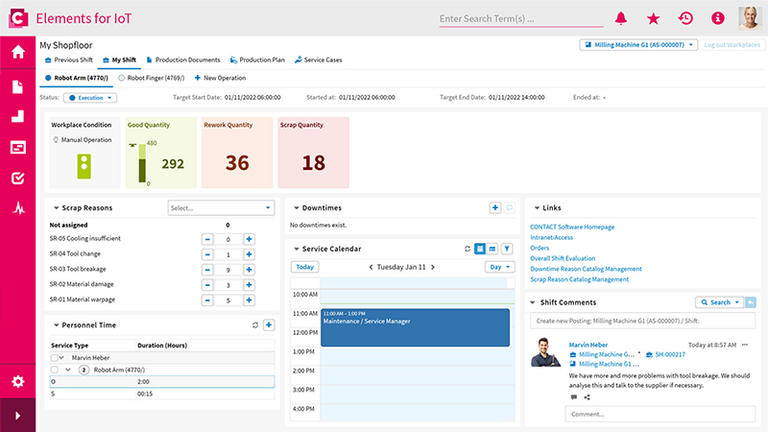
CONTACT's MOM solution supports your shift and personnel scheduling as well as machine assignment. This allows your production management to schedule teams for upcoming production orders in shifts and assign them to the corresponding machines.
With flexible shift systems, rotation profiles and substitution rules, you minimize personnel-related downtimes and optimize workflows with standardized shift handover processes. Machine operators are also efficiently supported: All production documents required for your tasks, such as drawings, process and safety instructions, can be found in one system.
Coordinate your production team efficiently and flexibly
CONTACT's MOM solution supports your shift and personnel scheduling as well as machine assignment. This allows your production management to schedule teams for upcoming production orders in shifts and assign them to the corresponding machines.
With flexible shift systems, rotation profiles and substitution rules, you minimize personnel-related downtimes and optimize workflows with standardized shift handover processes. Machine operators are also efficiently supported: All production documents required for your tasks, such as drawings, process and safety instructions, can be found in one system.
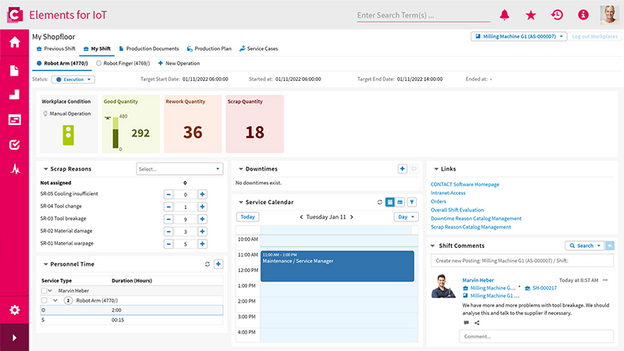
CONTACT's MOM solution supports your shift and personnel scheduling as well as machine assignment. This allows your production management to schedule teams for upcoming production orders in shifts and assign them to the corresponding machines.
With flexible shift systems, rotation profiles and substitution rules, you minimize personnel-related downtimes and optimize workflows with standardized shift handover processes. Machine operators are also efficiently supported: All production documents required for your tasks, such as drawings, process and safety instructions, can be found in one system.
Global multi-site support – simple and flexible machine connection
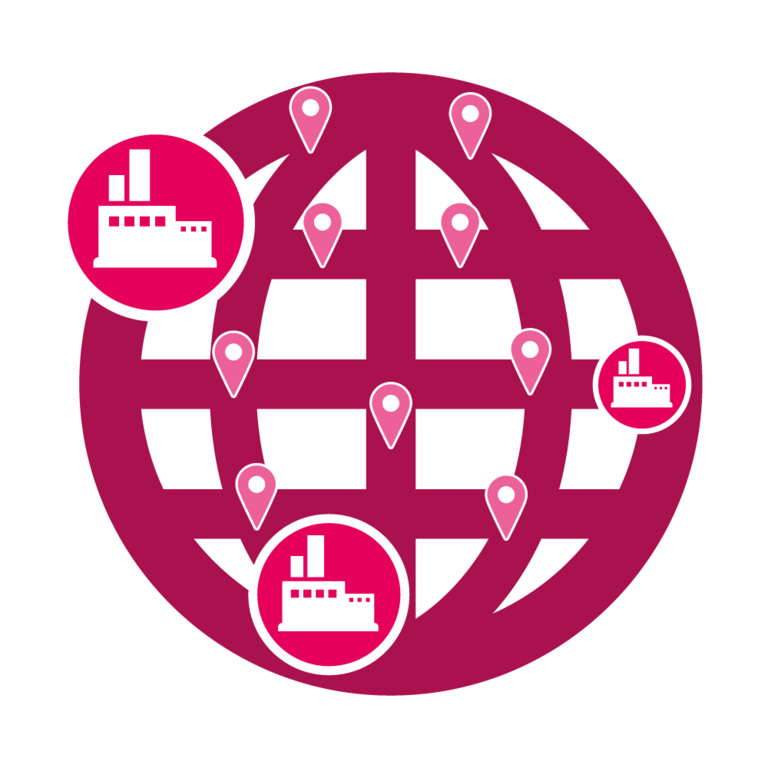
Thanks to multi-site support, CONTACTs Manufacturing Operations Management enables global analyses across all manufacturing sites and creates the basis for high system performance. Connect an administrative instance with operational instances close to the machines with the special multi-site architecture – ensuring low latency in the plants on site.
In addition, Elements for IoT supports MQTT and OPC UA, two key industry standards for easy machine connectivity to IoT platforms. If required, CONTACT implements further connectors for data exchange with production plants.
Global multi-site support – simple and flexible machine connection
Thanks to multi-site support, CONTACTs Manufacturing Operations Management enables global analyses across all manufacturing sites and creates the basis for high system performance. Connect an administrative instance with operational instances close to the machines with the special multi-site architecture – ensuring low latency in the plants on site.
In addition, Elements for IoT supports MQTT and OPC UA, two key industry standards for easy machine connectivity to IoT platforms. If required, CONTACT implements further connectors for data exchange with production plants.
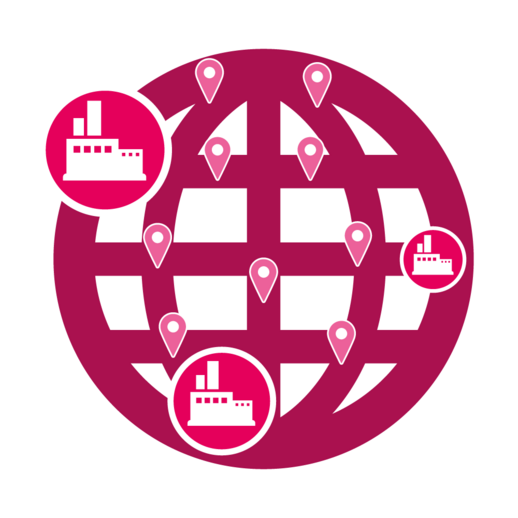
Thanks to multi-site support, CONTACTs Manufacturing Operations Management enables global analyses across all manufacturing sites and creates the basis for high system performance. Connect an administrative instance with operational instances close to the machines with the special multi-site architecture – ensuring low latency in the plants on site.
In addition, Elements for IoT supports MQTT and OPC UA, two key industry standards for easy machine connectivity to IoT platforms. If required, CONTACT implements further connectors for data exchange with production plants.
Global production control in real time
thyssenkrupp Dynamic Components is a worldwide leading manufacturer of powertrain components and a significant development partner of the automotive industry. Find out what added value the globally rolled out shopfloor management solution CPOS (Central Production Operating System) based on CONTACT Elements offers production employees and management.
Global production control in real time
thyssenkrupp Dynamic Components is a worldwide leading manufacturer of powertrain components and a significant development partner of the automotive industry. Find out what added value the globally rolled out shopfloor management solution CPOS (Central Production Operating System) based on CONTACT Elements offers production employees and management.
thyssenkrupp Dynamic Components is a worldwide leading manufacturer of powertrain components and a significant development partner of the automotive industry. Find out what added value the globally rolled out shopfloor management solution CPOS (Central Production Operating System) based on CONTACT Elements offers production employees and management.
Related Elements
Use the virtual representation of devices in the field for product and process improvements
Establish the digital twin as a database for all IoT business processes
Create complete profiles across the entire lifecycle of your products and map changes in the field
Use the digital twin as a basis for creating added value for your customers
Ideal coordination between tool design and product development
Make relationships between products and tools transparent
Shorten time to market by parallelizing design and work preparation
Avoid delays to the start of production and additional costs with integrated project management
Seamless integration of suppliers
Smooth the transition between product development and manufacturing with early work planning
Seamless transition between development and manufacturing thanks to work planning in the PLM system
Reliable transfer of the changes made to engineering BOMs to production
Direct transfer of work plans for processing production orders
From virtual product to smooth start of production
Transparency in the pre-series process thanks to matchless support
Map series startup process robustly and control it cost-effectively
Use prototype BOM to plan materials requirements precisely and to schedule
Record activities when constructing samples and performing trials and synchronize tools with production
Further Information
Would you like to find out more about this topic? Choose one of the following information offers.